Notre gamme de robots industriels à grande vitesse, à la pointe de la technologie, compte plus d'une centaine de modèles pour répondre à tout type d'application. Elle comprend des robots spécifiques à forte capacité, à portée étendue, des robots 7 axes extrêmement agiles, des robots double bras à 15 axes ou encore des cobots.
Des systèmes d’entraînement Yaskawa pour plus de performances
Des protections réutilisables pour roulettes de chaises afin d’économiser de l’emballage
L'économie des emballages est devenue un sujet d'actualité, même pour des objets volumineux tels que des chaises de bureau. Il suffit alors de recouvrir les chaises pendant le transport, ce qui évite l'utilisation de cartons encombrants, et ensuite de rouler les chaises pour les transporter. Pour s'assurer que ces marchandises arrivent intactes chez le client, les roulettes des chaises peuvent être protégées par des capuchons en plastique. Le spécialiste allemand Gross+Froelich de la fabrication de roulettes de chaises et de meubles s'appuie sur une technologie d'automatisation moderne pour placer ces capuchons de protection. Les servomoteurs et servovariateurs de la série Sigma-7 et un automate de la série SLIO de Yaskawa jouent un rôle clé dans ce processus.
L’idée de Gross+Froelich, c’est qu’un mobilier sur roulettes ne devrait pas avoir besoin d'être porté jusqu'au client alors qu’il est possible de le faire rouler. Mais dans ce cas, pour s'assurer que le produit arrive à destination sans aucune égratignure, les roulettes doivent toutefois être protégées. Les capuchons de protection en plastique sont une bonne solution. Après le transport, ils sont faciles à retirer et à recycler. Mais comment optimiser la mise en place de ces capuchons de protection sur des roulettes dans le cadre d’une production industrielle ?
Jusqu'à 36 000 capuchons par jour
Une roulette de chaise se compose essentiellement de deux roues individuelles, sur chacune desquelles est pressé un capuchon (image 1). Ce processus est réalisé de manière entièrement automatisée et à une vitesse considérablement élevée. Pour se faire, la société allemande Gross+Froelich utilise une machine fabriquée par le constructeur de machines Aramis qui fonctionne désormais avec des temps de cycle de 2,4 secondes suite à sa refonte avec les technologies servo de Yaskawa (images 3 et 4). Selon le modèle de roulette, cela signifie qu'en 24 heures de fonctionnement, jusqu'à 36 000 capuchons de protection sont appliqués de manière entièrement automatisée sur les roues, qui sont ensuite assemblées pour former la roulette complète plus loin dans le processus d'assemblage. Cela représente environ 10 000 capuchons de plus que ce que la machine pouvait faire avant la nouvelle conception en Yaskawa.

La puissance de l’électrique à la place du pneumatique
Seules deux modifications de la machine ont suffi à réduire les temps de cycle. La capacité de la table rotative d’indexage pour la mise en place des capuchons en plastique a été portée de quatre à huit postes d’assemblage. En outre, trois des entraînements pneumatiques installés dans la machine ont été remplacés par des servomoteurs électriques hautement dynamiques. Il aurait été pratiquement impossible d'atteindre des vitesses plus élevées avec des entraînements pneumatiques, car les contraintes mécaniques auraient été trop importantes. En outre, la consommation d'air comprimé est beaucoup plus faible, ce qui a un effet positif sur les coûts d'exploitation.
La série Sigma-7 de Yaskawa a été choisie pour la qualité de ses entraînements électriques qui ont déjà fait leurs preuves dans de nombreuses applications similaires et ont impressionné le constructeur de machines Aramis. En effet, la série Sigma-7 se caractérise notamment par une mise en service rapide, une capacité de production élevée et une fiabilité opérationnelle maximale. En outre, les servomoteurs très rapides présentent des dimensions extrêmement compactes et leur fonctionnement est très silencieux. Ils offrent une haute résolution (avec un codeur absolu 24 bits intégré) et une dynamique élevée. Les servovariateurs sont également compacts et intègrent des fonctions telles que la suppression des vibrations et des fréquences de résonance de la machine, ainsi qu’une fonction « auto-tuning » pour un démarrage simple.
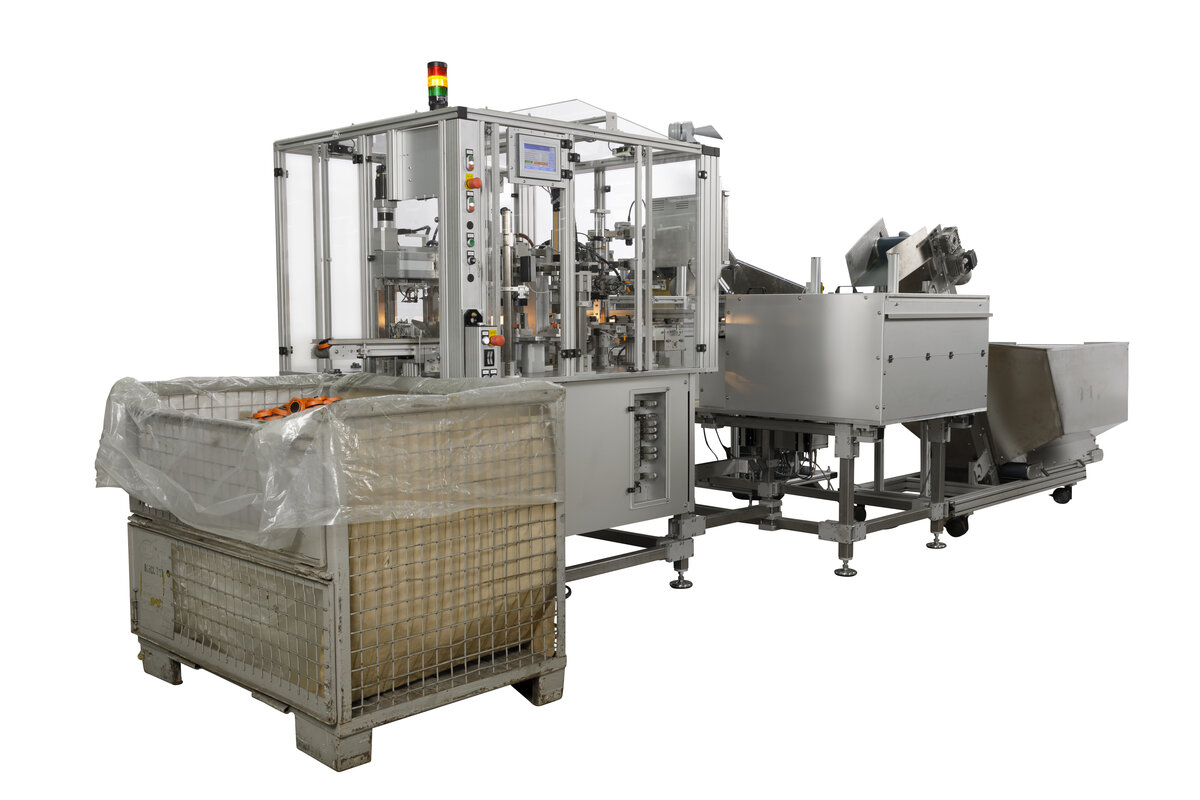
Le constructeur de la machine et ses différents partenaires ont collaboré avec les spécialistes en automatisation de Yaskawa pour adapter la machine au montage des capuchons de protection. Au total, trois axes servo de 400 V, chacun d'une puissance de 400 W, sont maintenant utilisés dans la machine. Un premier servopack est responsable du mouvement horizontal du système d'alimentation. Une unité linéaire pneumatique équipée d'une pince transfère le capuchon en plastique de l'unité de séparation vers le poste de dépose de la table d’indexage. Un cylindre électrique entraîné par un deuxième servopack presse le capuchon contre la roue de la chaise. Un capteur de contrainte détecte l'augmentation de la force lorsqu'il s'engage et avec le système de codeur absolu du servomoteur, ils détectent si le processus de pressage a réussi. Le troisième servopack commande le mouvement horizontal qui permet de déposer les pièces finies sur la goulotte. Les roues sont maintenant protégées de manière appropriée et acheminées vers un caisson de stockage afin d’être transportées ou stockées pour un assemblage ultérieur.
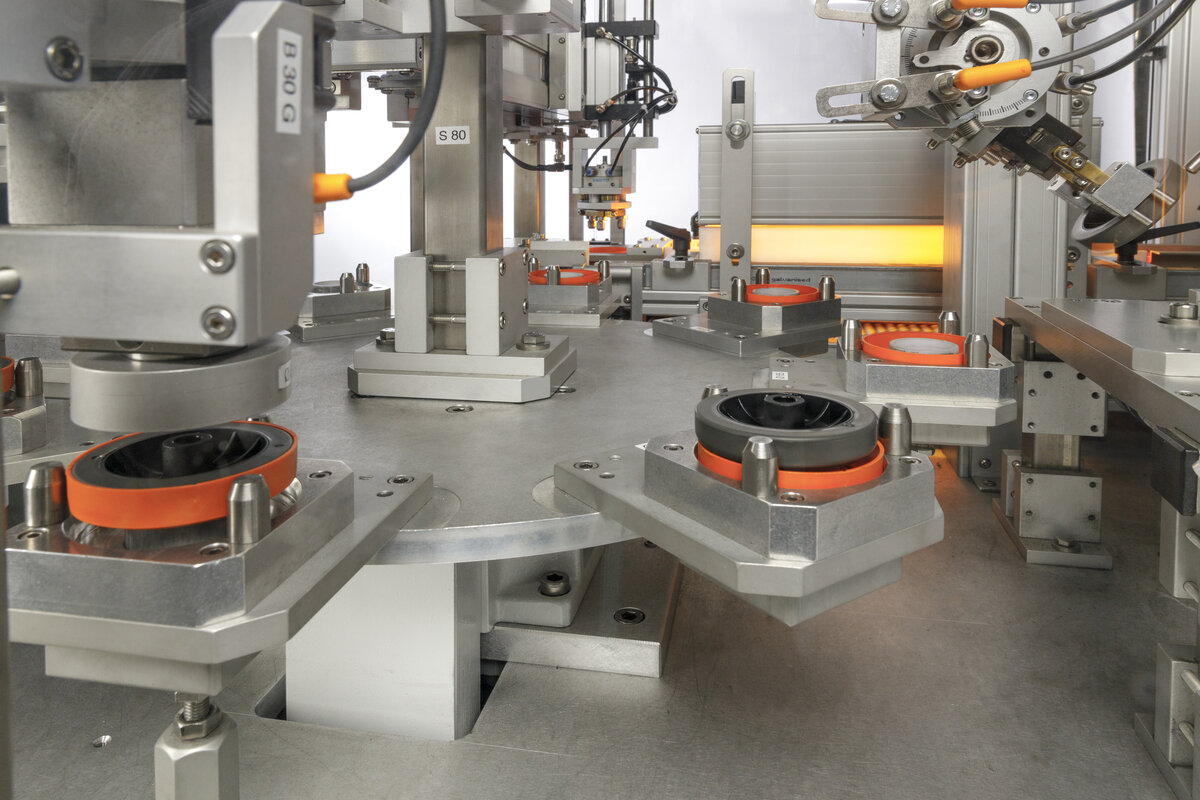
Entraînements, contrôleur et logiciel proviennent d’un fournisseur unique
Le contrôleur de la machine communique avec les axes servocommandés via Profinet. Le pilotage de la série d’automates SLIO, également fournie par Yaskawa, peut être programmé facilement dans Step7 de Siemens et peut être adapté efficacement à l'application grâce à sa conception modulaire (image 5). Il a été facile d'ajouter et d'interconnecter les modules d'E/S supplémentaires nécessaires. En principe, des extensions complémentaires sont également possibles. L’un des avantages en termes de vitesse est fourni par le bus de fond de panier du système d'E/S, qui fonctionne à 48 Mbit/s et permet une commutation indépendante du bus de terrain avec une précision de synchronisation de +/-1 μs. Les temps de cycle sont très courts pendant le traitement du programme et garantissent des séquences rapides. L'intégration de la vaste bibliothèque dans le système des contrôleurs simplifie également l'application, avec un grand nombre de fonctions disponibles qui peuvent être activées selon les besoins. Ceci est particulièrement utile lorsque l’on repense la conception de la machine originale, tout en conservant le bus de terrain existant. Le Profibus en est un exemple typique.
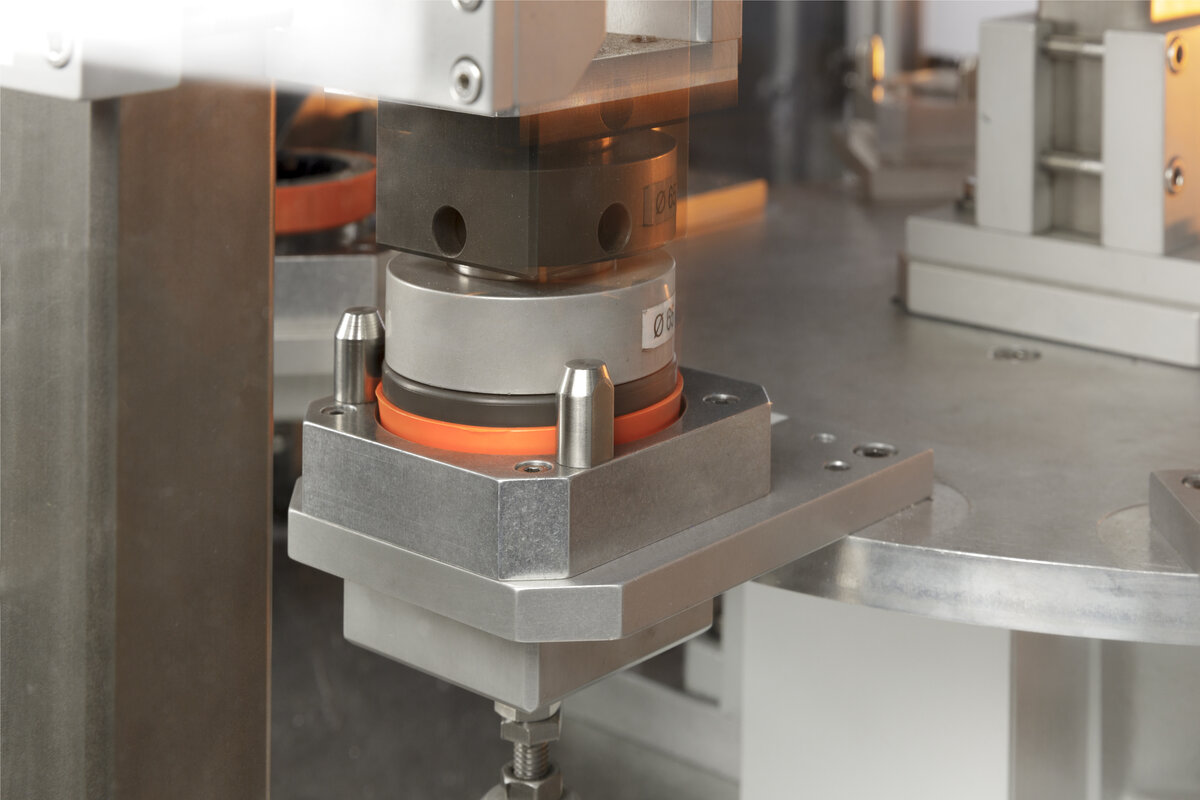
Les spécialistes Yaskawa ont également été d'une aide précieuse pour le constructeur de machines et ses partenaires en ce qui concerne l'adaptation des logiciels. Par exemple, ils ont aidé à intégrer la pneumatique, la vision et la communication avec le système de traitement d'images que Gross+Froelich utilise pour assurer la qualité de sa production. Grâce à ce principe de "fournisseur unique", la mise en service a été rapide et simple. Le matériel et le logiciel sont parfaitement adaptés l'un à l'autre et le constructeur de la machine n'avait qu'un seul interlocuteur. Personne n'a eu à se soucier des problèmes d'interface et cela a été un vrai gain de temps. Entre-temps, la machine modernisée et les composants qui y sont installés ont fait leurs preuves dans la pratique. C’est ainsi que sont désormais équipés de capuchons de protection d'innombrables roulettes de chaises chez Gross+Froelich. Les axes servocommandés hautement dynamiques de Yaskawa et son contrôleur compact SLIO y contribuent quotidiennement.